【イベントレポート】実践するスマートファクトリー ―製造DX責任者が事例で語る、AR/AI/IoTで実現するデジタル化メソッド―
23,000名(※2023年10月末時点)のプロの経験・知見を複数の企業でシェアし、経営課題を解決するプロシェアリングサービスを運営する当社では、毎月10回程度のウェビナーを開催しております。
2021年7月29日は、日々挑戦を続けるDX推進室・経営企画室・システム開発担当部門の方々に向けて、現役のDX責任者として工場における加工自動化、IoT・AI・ARの活用などを推進されている 佐藤氏に、スマートファクトリーのロードマップや推進のポイントをご紹介いただきました。
「スマートファクトリーに興味はあるが、何から着手したら良いかわからない」
「熟練工の高齢化などで必要性は理解しているが、DX推進に向けた社内の巻き込みができない」
こうしたお悩みを持つご担当者様は必見です。
当日参加できなかった方、もう一度内容を振り返りたい方のために内容をまとめましたので、ご参考になれば幸いです。
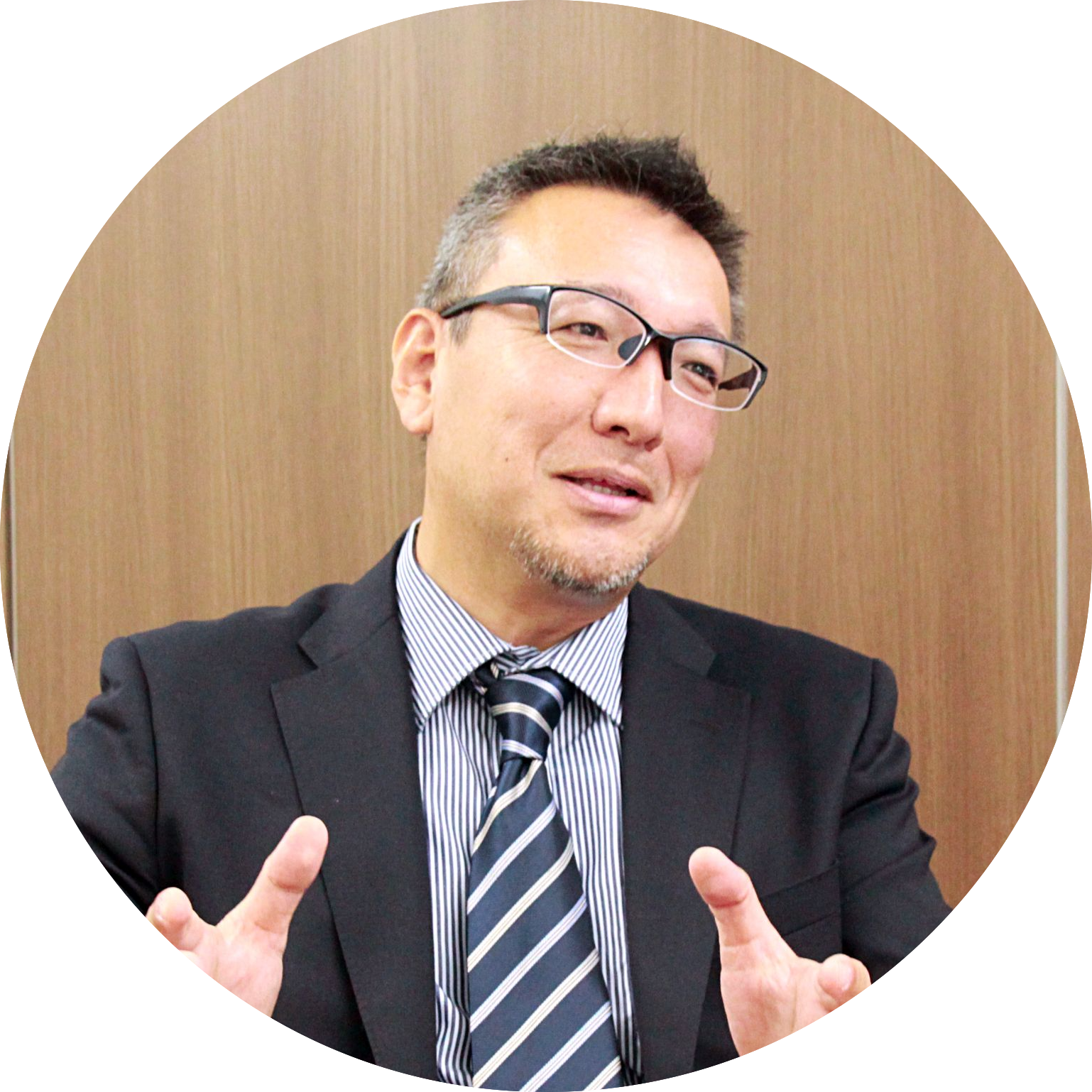
佐藤 賢一氏
株式会社JRC CDO 兼 デジタル・AI推進部長
東芝でグループ会社の物流・製造現場の生産統括責任者を経験後、株式会社JRCの最高デジタル責任者 兼デジタル・AI 事業部に就任。工場における加工自動化や、IoTフラットフォーム・ AI・ARを活用したデジタルツイン構築など全社DXを責任者として推進中。
.png)
松井 優作
株式会社サーキュレーション プロシェアリング本部 マネジャー
早稲田大学卒業後、新卒一期生で創業期のサーキュレーションに参画しマネジャー就任。首都圏を中心に自動車や大手製薬メーカーなど製造業50社以上に対し、全社DXの推進・新規事業開発・業務改善・営業部隊の構築・管理部門強化などの幅広い支援実績を持ち、実行段階に悩みを抱える企業の成長を支援中。
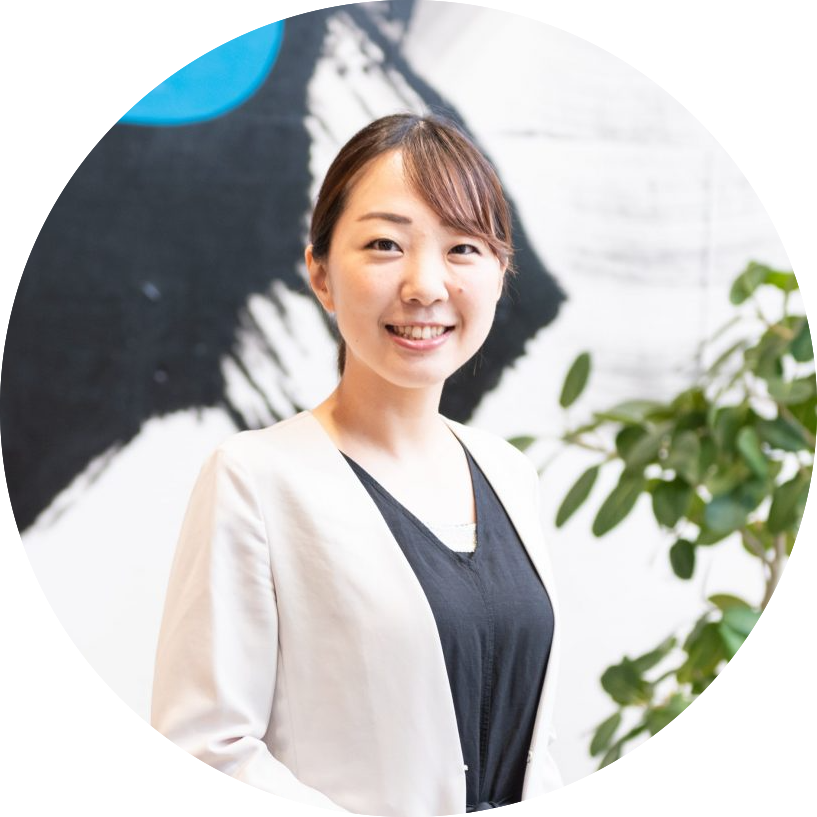
新井 みゆ
イベント企画・記事編集
新卒で入社した信託銀行では資産管理業務・法人営業・ファンド組成の企画業務に従事。「知のめぐりを良くする」というサーキュレーションのミッションに共感し参画。約1500名のプロ人材の経験知見のアセスメント経験を活かし、サービスブランディング、イベント企画等オンライン/オフラインを融合させた各種マーケティング業務を推進。
※プロフィール情報は2021/7/29時点のものになります。
Contents
製造業において課題解決の鍵となるスマートファクトリーの推進
外部環境の変化によって変革が求められている製造現場
現在の製造業には、さまざまな課題がのしかかっている。人口減少による労働人口の不足をはじめ、コロナ禍も含めた外部環境の激しい変化、そしてAIやIoT、VRといった新しいテクノロジーの活用など、枚挙にいとまがない。顧客ニーズの多様化にそなえ、従来の大量生産から少量多品種生産への対応を迫られている企業も多いだろう。
また経産省の「2021年版ものづくり白書」によれば、製造業のニューノーマルは「レジリエンス」「グリーン」「デジタル」が主軸となるとされている。
これらの変化に対応し、持続可能な経営体制の構築をすることが、製造業においては急務だと言える。
製造業DXが目指すデジタルツインとは?
「ものづくり白書」が唱える「デジタル」領域で主眼となるのが、DXだ。日本においては第四次産業革命が謳われており、各国でも製造業のデジタル化に向けた取り組みは加速している。
その中で製造業DXが最終的に目指すべき地点については、「デジタルツイン」という言葉が鍵となる。
デジタルツインとは、簡単に言えば現実世界――物理空間で収集したデータを基に、設計から販売までのプロセスをデジタル上でも「双子のように」再現する技術だ。これによって、不良品率や作業工程の改善、新規サービスの立ち上げなどが容易になる可能性がある。
デジタルツインはスマートファクトリーの文脈で語られることが多い概念であり、スマートファクトリー化の一部に、デジタルツインへの取り組みが含まれるのだと言える。
自動化の導入ハードルが高いディスクリート型工場が抱える悩み
では、デジタルツインも含めスマートファクトリーを実現するにはどうすべきなのか。今回は製造業の工場の中でも、特に組み立て型の工場――いわゆるディスクリート型について取り上げる。
ディスクリート型の特徴は、人手が必要な工程が多いことだ。いわゆる熟練工の技術に頼る部分も多く、液体処理を主とするプロセス型に比べると自動化の難易度は非常に高い。そのため、多くの製造企業が「何から手を付けるべきか」と頭を悩ませているのだと言える。
JRCの事例で学ぶ、AR/AI/IoTを活用したスマートファクトリーの実践
今回ご登壇いただいた佐藤氏は株式会社JRCの最高デジタル責任者であり、前述したようなデジタルツインをはじめ、全社的にDXを推進しているスマートファクトリー化のプロだ。今回は実際にJRCの事例をご紹介いただきながら、スマートファクトリー推進のポイントを探っていく。
ディスクリート型製造業の中堅企業として知られるJRC
JRCはベルトコンベヤ部品のトップブランド企業として知られており、主な取り扱い製品はコンベヤ用プーリ、ローラなど。プーリとローラの売上シェアは、2018年度時点で約50%と圧倒的だ。工場は全国に4拠点展開している。
ディスクリート型製造の中堅企業であるJRCに佐藤氏がジョインしたのは、2019年。現在は特に、金属加工の分野において、製造現場のデジタル化に取り組んでいるという。
Excelで月報を作っていた状況から一転、リアルタイムで工場のデータを蓄積
ここでは、佐藤氏がジョインされた当時のJRCと現状、そして未来に向けた動きについて簡単にご紹介いただいた。
佐藤:例えば金属加工にはプレスや切断などの工程がありますが、これまで設備はそれぞれスタンドアローンで動いており、稼働状況は1日1回USBで取得。Excelにまとめて月報を作っているような状況でした。現在はPLC(プログラマブル・ロジック・コントローラ)から主要工程の設備の品質や数量情報をリアルタイムに得て、活用しています。
将来的には人も含めてさまざまな工場のデータをリアルタイムで見られるようにして、品質や生産性向上、原価管理など多目的な活用をしていきたいと考えています。いわゆるデジタルツインの構築と、そのデータ活用によるスマートファクトリー化ですね。
工場のデータを取得することで進捗管理なども簡単に行えるように
JRCのスマートファクトリー推進の取り組みのひとつが、前述でも触れたような工場の稼働状況のリアルタイム計測だ。実際に、以下のような画面で表示されるようになっている。
佐藤:これは生産数量の進捗画面ですね。基幹データから計画データを取得し、2段目に現在の生産台数を表示し、一番下で差異を算出しています。
一般的な進捗管理画面ではありますが、今まではこういったものを専用システムとして開発してきたことが多いと思います。しかしこれは、「IoTで工場のさまざまなデータをリアルタイムで取得したことで、進捗管理画面を副次的に簡単に作れた」という例です。
スマートファクトリー推進の初期フェーズで目指すべきレベルとは?
IoTで工場のあらゆるデータを取得し、情報の見える化や生産性・品質向上を目指す――。言葉にするのは簡単だが、実際にスマートファクトリーを推進するとなると、一体どこまで何を実施すべきなのか、指針に迷う。
そこで今回は、スマートファクトリー推進の段階を3レベルに分け、初期フェーズで目指すべきレベルについて教えていただいた。
松井:これまでは生産性や品質の向上、コスト削減を目指して局所的にIoTやデジタルツールを導入することが多かったと思います。一方で佐藤さんのお考えとしては、「将来的にどうサステナブルな事業を作っていくか」という目線に立って、スマートファクトリーを推進していくべきとされているそうですね。
佐藤:レベル1のカイゼンは、従来から日本の製造業が得意としてやってきました。DXやスマートファクトリーがカイゼンと違うのは、レベル2以上のことが技術的にもコスト的にもできるようになったことです。実現のハードルが下がったわけですから、社会問題である人手不足に対して手を打たなければならない。これがDXの本質かと思います。
ただ単に工場としての生産性や品質を上げるのではなく、将来まで見据えて人材の活用や技能の継承、リスク管理の強化を図る。これが、スマートファクトリー推進の第一歩となる考え方だ。
停滞しないスマートファクトリーの推進メソッド
ここからは、実際に佐藤氏がどのような手順で事業サステナブルを目指したスマートファクトリー推進を行っていったのかをご紹介していく。メソッドはまずは大きく、2つのフェーズに分けられる。
フェーズ1は「スマート化戦略策定」、フェーズ2は「デジタルフィッティング」だ。それぞれのフェーズにおけるポイントは、3つのステップ、3つのサイクルで説明ができる。
【前提】戦略策定とツール導入時に発生する6つの課題
解説に入る前に把握しておきたいのが、以下の6つの課題だ。これらは戦略策定及びツール導入時に、多くの企業が陥りやすいケースだという。
松井:例えば戦略策定においては部分最適の改善に留まってしまったり、推進者に丸投げしてしまったりするようですが、JRC様に限らずさまざまな企業のご支援をされている佐藤さんからすると、これらはよくあるポイントなのでしょうか。
佐藤:そうですね。何かやりたいときは安く、小さく始めたりトライアンドエラーをしたりすべきではあるのですが、やり方によってはそこで止まってしまい、次につながらないパターンが多いです。
松井:戦略策定後は外部ベンダーを巻き込みながらツールを開発すると思うのですが、ここもいかに要件を整理するかが重要なんですね。
佐藤:ベンダーさんは事業については詳しくありませんからね。いかにそれを伝えられるのかはコミュニケーション次第です。私がずっとやってきたのは、トップと現場、内部と外部のブリッジですから、非常に大切です。
3つのステップと3つのサイクルは、上記6つの課題を解決するものでもある。どのように問題を回避するべきなのかと併せて、詳細を解説いただいた。
スマート化戦略策定フェーズにおける3ステップ
STEP.1目的の明確化を行う
戦略策定における最初のステップは目的の明確化だ。ここで陥りがちなのが、目的をひとつに絞りきれないという状況だという。ここについては、佐藤氏も大きな課題感を抱えながら推進したと語る。
佐藤:特に大きな企業は階層が多くなるので、トップのニーズや意思に対して現場がやりたいことにもギャップがあります。そこをどう埋めていくかが重要ですね。
松井:JRC様の場合は、どのように乗り越えていったのでしょうか?
佐藤:JRCの場合はトップが明確なビジョンを持っているのですが、「そうは言っても急にはできない」という現場とのギャップを埋めるのが非常に難しかったです。解決のためには、やはりそれぞれの階層の人とよく話をして、トップや現場がどうしたいのかを知ることです。
STEP.2社内体制を構築する
次の体制構築について肝要なのは、推進者に丸投げするのではなく、現場を巻き込んだ全社プロジェクトにすることだ。ここでは、外部のプロ人材の活用も視野に入れる必要があるという。
佐藤:体制全てを外部人材で構築してしまうとリスクや課題が生じるので、少しずつ内部人材を増やしながら、自社に合ったパートナーを選ぶことが大切だと思います。
松井:JRC様ではどのようなプロジェクト体制になっているのでしょうか?
佐藤:私が所属する推進部門と工場が連携する形にしています。あとは経営企画室ですね。月に1度は、社長へのインプットとヒアリングもしてもらうような体制で進めています。
STEP.3構想の策定をする
体制の目処が立ったら、いよいよ構想の策定に入る。
すでにITツールを一定導入している方は実感があるかもしれないが、現在はデジタルツールと一言に言っても非常に種類が多く、どこに何をどれだけ投資すべきなのか、判断に迷うシーンが出てくる。この点について佐藤氏は、3~5年をかけて分散させた投資設計が必要だとする。
佐藤:スマートファクトリーの最終形であるデジタルツインの達成は、すぐにできるものではありません。投資するにしても、何千万、何十億円とかかる可能性もあります。
そこまでの資金力がある企業は限られますから、まずは中期計画を作り、少しずつ進めていくのがおすすめです。
松井:JRC様では何ヵ年のマイルストーンを敷かれたのでしょうか?
佐藤:2015年の崖を一区切りとして、どう5年後を目指すのか、その2年前にどんな姿であるべきかを描きました。2~3年の中期計画は、半年~1年ごとに軌道修正しています。
デジタルフィッティングフェーズにおける3サイクル
CYCLE.1IoTツールの要件定義をする
戦略策定が完了したら、次はデジタルフィッティングのフェーズに入る。ここで実施すべき最初のサイクルは、要件定義だ。
松井:ここでは要件定義ができるスキルを持っていることが非常に重要だと思うのですが、JRC様の場合は、佐藤さんが現場からの意見を吸い上げながら、どんな要件で開発してもらうのかをベンダーさんにお願いしたのでしょうか?
佐藤:そうですね。ただ、システム化による業務効率化なんかはまとめやすいのですが、業務プロセスの改革の要件定義をきちんと工場の現場でオーソライズするのは非常に難しいです。
非常に良い技術を持ったベンダーさんはたくさんいるので、やはり現場と技術の間をブリッジして、技術をどう現場に適応させるのかを考えるのが一番のポイントになります。
CYCLE.2データの収集・活用を行う
実際にシステムを運用する段階になったときに生じるのが、データの精度が悪い、安定した収集ができないといった課題だ。しっかりと要件定義をした上であっても、現場で運用すると理論通りにはいかないと佐藤氏。
佐藤:理論的には「PLCによって設備からこういうデータが取れる」ということになっているのですが、欲しいタイミングで正確に取れるかというと、そうではない場合があります。例えば振動や電流データというのはデータとして使う前にクレンジングが必要ですし、通信環境やセキュリティの問題が生じることもあります。
松井:いろいろな落とし穴があると。
佐藤:かといって最初から堅牢に作るとコストがかかってしまうので、ある程度エラーを前提としてスモールスタートし、実際にやっていけそうだと実証できたら強化していくやり方がいいと思います。
CYCLE.3システムの評価・改善を行う
上手くいかないことを前提としてシステムを評価し、改善を繰り返す――これが、まさに最後のサイクルに該当する。
松井:佐藤さんは改善サイクルをどの程度のタームで回しているのでしょうか?
佐藤:半年で回すものもあれば、横展開を前提として1~3ヶ月のサイクルで回す場合もあります。プレスで上手くいったら、溶接にしようといったケースですね。
松井:課題としては「本番運用に切り替える判断時期がわかりにくい」とありますが、これは具体的にどういった状況なのでしょうか。
佐藤:「収集・活用」サイクルでお伝えしたことと関係がありますが、やはり安定的にデータを取得できるハードウェア構成や環境になっていない場合があるんです。「今日はデータが取得できていないぞ」と思ったら、電源が抜かれていたなんてことも起こります。安定化させるには運用プロセスを定義し、これを工場のメンバーがきちんと理解する必要があります。
実践するスマートファクトリーまとめ
今回のウェビナーのポイントを、以下の3点にまとめた。
今回ご紹介したウェビナーで使用した資料は、未公開部分も含め以下のリンクからDLできます。実践するスマートファクトリーにご興味を持たれた方は、ぜひご活用ください。