東芝出身の工場経営のプロ南波正司氏が中小紙器工場の在庫金額30%削減を達成。工場改革の道のりとは?
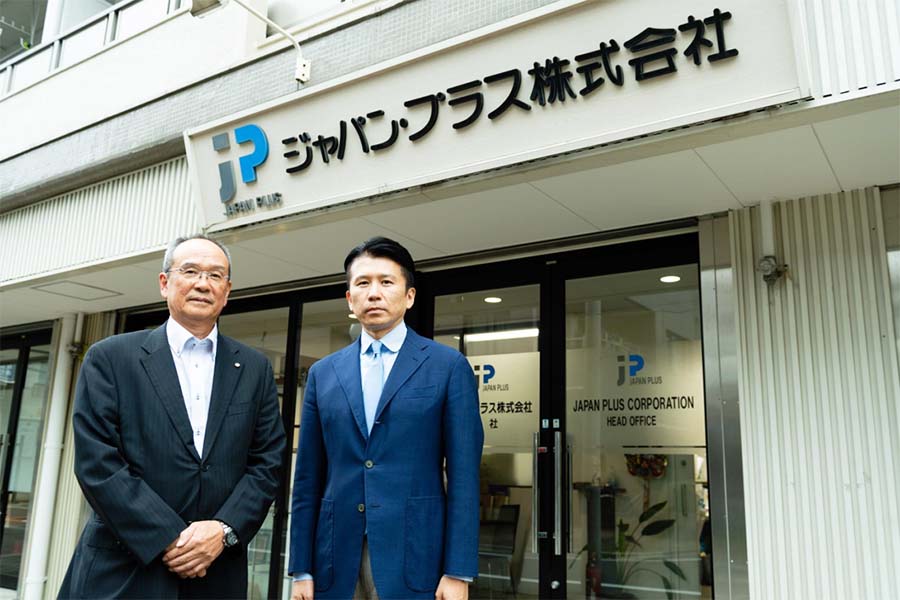
長年、プラスチック真空成型品をメイン事業としてきたジャパン・プラス株式会社。同社の紙器工場は20年前にスタートして以来旧態依然の生産体制のままで、在庫過多という課題を抱えていました。工場経営をアップデートするため、同社は東芝の子会社で工場長も務めたことのある南波正司さん(以下:南波)に支援を依頼。成果が出るまでの3ヶ月間にフォーカスして、支援内容を専務取締役笠倉大二郎さん(以下:笠倉専務)との対談形式でご紹介します。
Contents
旧態依然の工場の問題点を洗い出し、適切な生産計画を立てたかった
ポリ袋の製造から事業をスタートし、真空成形を主軸に事業展開。20年前から紙器にも事業を拡大
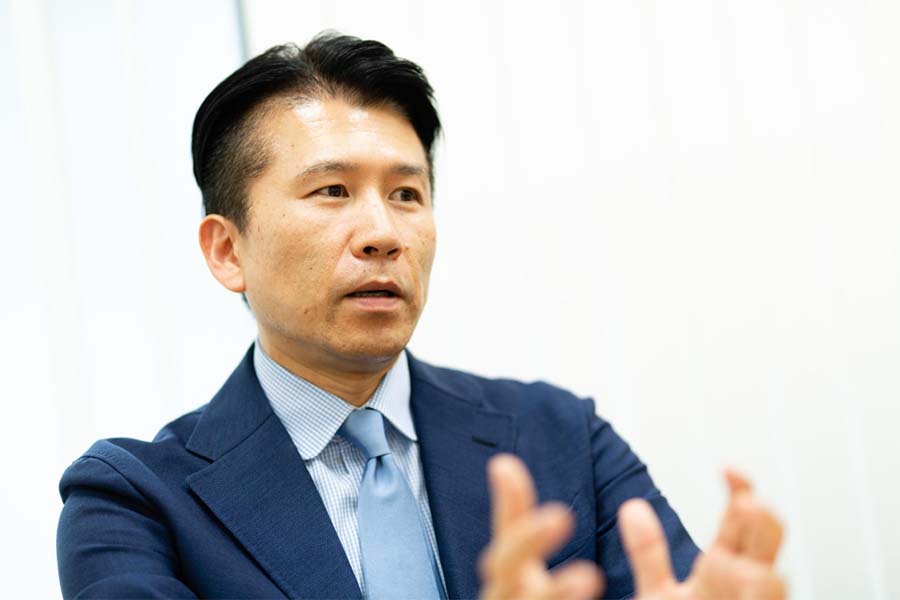
笠倉専務:ジャパン・プラスは私の父が創業した会社で、最初はポリ袋の製造からスタートし、その後真空成形(プラスチックシートをヒーターの熱で軟化させ、様々な形状に作成した金型を用いて真空引きを利用して成形する技術。成形後、冷却することで固化させて成形品を作成する)を主軸に事業を展開しました。20年ほど前から紙器(商品の収納や包装に用いられる紙製容器)・梱包資材の加工も始めました。私は当時全く業種の違う大手メーカーで海外人事の仕事をしていたのですが、新事業の立ち上げを手伝わないかと言われて転職し、現在は専務を務めています。それ以降は営業責任者、広報及び開発の役割を担っていました。
社員も専務も実感していた、営業と工場が上手く意思疎通できていない現状
笠倉専務:課題を抱えていたのも、その紙製品を扱う紙器・梱包資材工場ですね。20年前は世間的にかなり需要が高く、残業や休日出勤もして稼働していたくらいでした。20年経過した今は生産数・インフラも落ち着いてきました。大量生産から小ロットの受注生産に徐々にシフトしていたのですが、製品の作り方も現場の作業工程も、ほとんど変えていませんでした。適切な生産計画が無く、とにかく注文があればすぐに材料を発注して工場で作るという体制だったため、工場には材料や製品が溢れかえっていたんです。
また、社員が退職する際はいつも会社の至らなかった点をヒアリングしているのですが、そこで「工場の旧態依然」という指摘がありました。私自身も感じていた課題ではあったのでショッキングでしたし、やはり工場の問題点を明確にして現場の改善を図っていくべきなのだと痛感しました。
しかし、私には工場運営の経験もノウハウもありません。調べようとしても体系化された書籍は無く、講習会やセミナーが開催されているわけでもありませんでした。困り果てて埼玉県プロフェッショナル人材戦略拠点に相談してみたところ、最近では外部人材を招いてスピーディに経営改善するという方法があると教えてもらいました。
もちろん採用も考えたのですが専門知識のある方と知り合う機会もないですし、その他の知識を得る方法も散々検討した後だったので、いただいたアドバイスをもとにプロ人材の起用を決断しました。
面談と工場見学を行なった際、「宝の山」と言って一番前向きに改善案を提案してくれたのが南波さんだった
笠倉専務:複数のプロシェアリング会社を紹介してもらい、各企業の担当者には、当社の課題感や私の考えをお伝えしました。その中から3社ほどに絞った段階で実際にプロ人材の方々と面談をして、工場見学もしてもらいました。旧態依然の工場ですから、現状に対して呆れたような態度を見せる方もいましたよ。私はそんなリアクションも受け止められますが、現場で働いている人間に伝わったらスムーズな改善はできないだろうと懸念を抱きました。
その中で、こちらの課題に対して一番前向きな提案をしてくれたのがサーキュレーションさん経由でご紹介いただいた南波さんだったんです。南波さんは現場で長く働いていた方ですから経験者としての安心感もありましたし、この人なら適切にコミュニケーションを取ってくれそうだと感じてご依頼を決めました。
まずお願いしたのは、問題の見える化と生産計画の数値化です。現場にはモノが溢れていて、個々の仕事量が平均化されていませんでした。そんな現状の問題点を洗い出し、どんな生産計画が適切なのかを知りたいと思いました。
日本と中国を行き来しながら、中堅メーカーの現場に入り込み本質的な課題の解決に取り組む南波さん
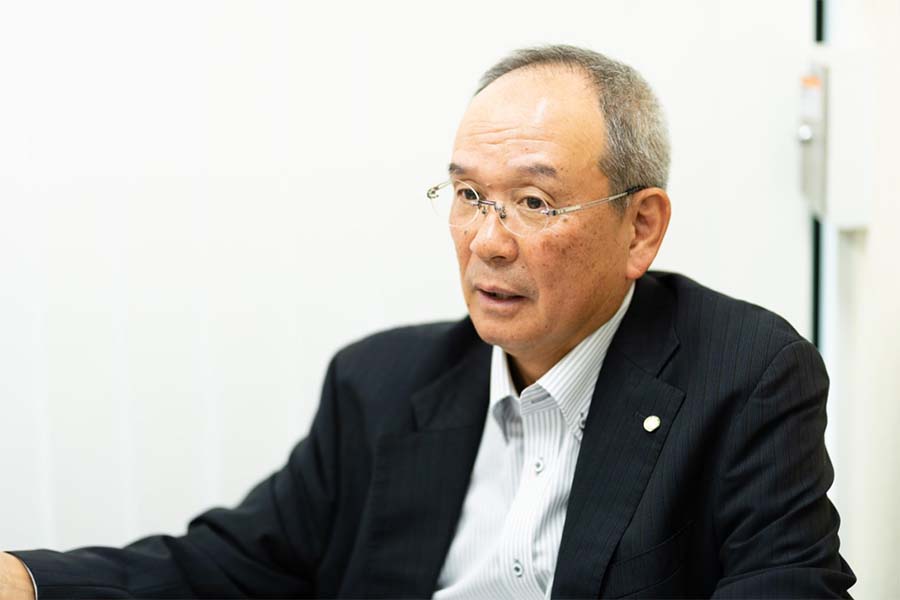
南波:私は東芝の照明事業会社の本社経営変革推進室で全工場・支店の社員教育とシックスシグマ改善活動などを主導しました。その後、同社の製造関係会社の沼津工場で工場長として工場運営、次に海外(中国/韓国/タイ)の品質・生産性改善、中国現法製造会社の立上支援などを経験し4年前に独立しました。現在は中堅メーカーに対して製造管理や品質、生産性向上を中心としたコンサルテング業務を行なっています。日本のみならず、中国の企業を支援することもありますね。日中技術交流センターを通じて、昨年は台州、今年は山東省のシ博市などを訪れました。国を挙げて産業政策を行なっていますから、中国の企業は活気がありますよ。
支援の強みとしているのは、実際に現場に入り込んで問題点を抽出し、「情報とモノの流れ」「同期化・整流化」を実践的に指導することです。流れとしてはまず現場の改善、それから仕組み改善というステップで取り組んでいます。それから、私は器用な方ではないので、ご支援する企業数は極力1~2社に絞り集中できる時間を作るようにしています。
課題抽出から新しい生産管理体制の構築、現場の浸透まで推進。支援から3ヶ月で効果を生んだ
まずは課題を洗い出し、現場にモノが溢れていた原因を特定。生産管理情報の一元化が目下の改善点だとわかった
南波:ジャパン・プラスさんの支援を決めたのは、たまたまスケジュールが空いていたこともありますが、『宝の山ともいえる解決すべき課題が沢山あるな』と思いました。
支援は週に1回ペースでスタートしました。といっても現場で行きあたりばったりのご支援をするわけにはいきませんから、稼働していないときも基本的に次の訪問に向けた戦略を練っていましたね。トータルで10ヶ月にわたる支援になりました。
支援はまず、工場の課題をチェックすることからスタートしました。現場にモノが溢れている原因は何なのか、私や専務、そして現場のメンバーもしっかり認識しなければいけません。工場にある現物が存在していますから、これらがどういう過程で作られたのかをしっかりヒアリングしました。誰がいつどんな指示で作り、なぜ工場に保管しているのかということです。
結果として、原因は生産管理情報が一元化されていない点にあることがわかりました。例えば営業は1ヶ月後に納品する案件などを取ってくるわけですが、注文が入った時点で材料を発注し、いつ作るのかは完全に現場任せでした。工場はたとえ1ヶ月先の納期でも材料があればすぐに製造してしまいます。現場に入ったらとにかく仕事をしなければ、という考えがあるからですね。大量生産の時代ならそれでも在庫は捌けるので問題がなかったんです。それがそのまま慣習として続いていました。
笠倉専務:当然のことながら材料が無くなれば従来の調達ルーティンワークとして、新たに材料をまた仕入れます。この結果、発注と製造と出荷のつじつまが全く合わず、会社としては毎月の支払いだけが増えてしまっていたんです。
南波:そうなると会社の財務管理に問題が発生します。今はキャッシュフロー経営の時代ですから、余計な在庫があって資金回収ができないと、運転資金が減るばかりです。最悪、会社が倒産します。さらに詳しく言うなら原価の問題ですね。材料の原価は10円でも、加工すると付加価値が生まれるので50円になります。これを会社で数ヶ月も保存すると、それだけで損害になります。製造業で作りすぎは禁物なんです。
3ヶ月かけて、20年間続いてきた考え方と作業工程を変更。極力在庫が発生しないような新しい仕組みを現場と共に作り上げた
南波:状況を打破するためには、教育するしかありません。これまで営業や工場のメンバーが良かれと思って続けてきた行動が実は会社を苦しめていたのだと教えて、働き方を改めてもらう必要がありました。そこで、笠倉さんにプロジェクトリーダーを数名選出してもらい、プロジェクトの施策を検討しながらまずはリーダーたちに考えを切り替えてもらうことにしました。
その上で、工場の仕組みも変更しました。材料は製造日の前日に納入することを基本として、余分な材料は持たないようにしたのがまず一点です。さらに製造前にきちんと計画を立て、誰が何を作っているのか、指示内容をメンバー全員が把握できるようにしました。当たり前ですが、個人の勝手な判断でモノを作らないということですね。営業は材料の発注を行わず、工場に対して受注情報だけを渡してもらうようにしました。
ここで重要なのが、なぜその仕組みで動かなければならないのかを現場のメンバー全員にわかってもらうことです。そこは指揮系統をはっきりさせるためにも、プロジェクトリーダーから伝えてもらうようにしました。
笠倉専務:リーダーたちもこういう変革は初めてで、説明できるようになるには3ヶ月ほどかかりましたね。現場も新しい仕組みに対して半信半疑なのでリーダーに意見を言うのですが、それに対してリーダーもなかなかロジカルに伝えられないんです。頭で理屈はわかっていても、上手に伝える技術までは身についていませんから。どうしようもなくなったら私が改めて説明をして問題解決をしていきました。一歩一歩階段を上がるような感覚でしたよ。
作り上げた仕組みをどうデジタルに落とし込むのかという部分も、やはり3ヶ月ほどかかっています。エクセルに受注や材料、出荷済み製品、在庫などの数を入力して引き算する程度のものではあるのですが、最初はなかなか良いものができなくて。最終的に私が作ったテンプレートをベースに運用することになりました。
現品票による材料や製品の管理も徹底。現場の状況を完全に「見える化」して、製造工場の本来あるべき姿を目指した
笠倉専務:仕組みが浸透しはじめたので、4ヶ月目以降は在庫をどれくらい減らしていけるかを調整していきましたね。また、現品票(製造現場などにおいて生産管理のために使われる伝票の一つ)による現場の材料や製品の管理もスタートしました。
南波:現品票をつけると現場にあるモノが「見える化」されて、要不要を判断できるようになります。例えば必要なのは明日や明後日使うモノで、不要なのは翌週や1ヶ月先に使うモノです。きちんと定義をしておけば、個人の感覚的な判断は不要になります。
定義の仕方は簡単で、工場が1日に生産できる量をもとに1週間で何をどれだけ作るのか決めてしまえばいいんです。必要な材料はその分だけです。働いているパートさんの人数は突然増えたりしませんからね。1日あたりの材料を1時間ごとに仕分ければ、何がどれくらい遅れているのか、その日の進捗状況もわかります。これが製造工場の本来あるべき姿です。
仕込生産品の在庫金額は30%削減に成功。現場の生産性に対する意識も大きく変化
笠倉専務:支援いただいてから3ヶ月で数値的な成果も出はじめて、仕込生産品の在庫が30%も減りました。金額に換算すると年間600万円相当です。実際には受注生産品の在庫も減っているので、さらに大きな数値になるはずです。
仕込生産品の数字を出してみると、実は受注生産品の在庫が足を引っ張っていることも新たにわかってきました。これも「見える化」の成果ですね。受注生産品は基本的にお客様からオーダーをもらってから材料を調達して作りますから、長く滞留しているはずはないと考えていました。現在は受注生産品の在庫を減らすことに注力しています。
さらにKPIやKGIを設定して、工場が改善すべき数値も明確に定めています。今までは何をどう測れば良いのかもわかっていませんでしたから、南波さんに教えていただいて非常に助かりました。紙器工場全体の損益や在庫の金額、保有日数、納期遵守率、着工遵守率は毎月報告しているので、メンバー全員が工場の状況を理解し、コスト意識も感じているようです。
また、現品票に対する意識も支援から1年経過して大きく変わりました。最初は『なんでこんな面倒なことをしなければいけないんだ』と言われていたものが、現在は工場になくてはならない存在になっています。現品票がいかに自分たちの生産に直結しているのかが見えてきたからですね。
スタートこそ大変だったものの、支援を通して得た文化は企業の大きな資産となった
苦労を乗り越えた先に新たな工場文化が生まれ、現場にしっかりと根付いたのは南波さんのおかげ
笠倉専務:なかなか現場に理解してもらえないことも多々あり、スタートしてからの3ヶ月は大変でした。最初は数値的な成果も見えませんでしたから、正直を言えば苦しかったです。
それでも、数値に変化が見えると現場の雰囲気はガラッと変わりました。現品票をつけるかどうかも議論があったのに、今は『現品票が無いのは工場としてありえないだろう』という話にまでなっています。支援は約10ヶ月でしたが、この間で新たな企業文化、工場文化が生まれたことには非常に感謝しています。
南波:現場は多かれ少なかれ宝の山ですが、今回は大きな宝の山がありましたね。
私個人として勉強になったのは、取り組み内容の伝え方です。同じことを伝えるにしても、例えば子供と大人とシニアに対しては、言い方が変わりますよね。支援の要となるのは現場の人達ですから、どう組織に合った伝え方をすればいいのか、非常に考えさせられました。
ジャパン・プラスさんには今後も工場のグランドデザインを描いて、どう進むべきかを考えて更に変革していってほしいですね。
プロ人材を紹介する側も、要望をきっちり伝えやすくするためにフランクな雰囲気作りをしてくれた
笠倉専務:南波さんはもちろん、サーキュレーションの担当者である土井さんにフランクな雰囲気を作っていただいたので、こちらの要望は全てお伝えできたと思っています。週に1回の支援日には南波さんにせっかく来ていただくので、ディスカッションをセッティングしてもらいました。
南波:サーキュレーションさんには良い企業を紹介いただいて感謝しています。日本にはいろいろと悩んでいる企業がもっと多いはずなんですよね。今後もそういった企業と上手くマッチングしてもらえたらと思います。お互いにwin-winですから。
支援スタートから3ヶ月間は苦しい時期だったというジャパン・プラスさん。それでも成果が出ることを信じてプロジェクトを進めることができたのは、最初に南波さんに感じた信頼感があったからなのかもしれませんね。
本日はお忙しい中、ありがとうございました!
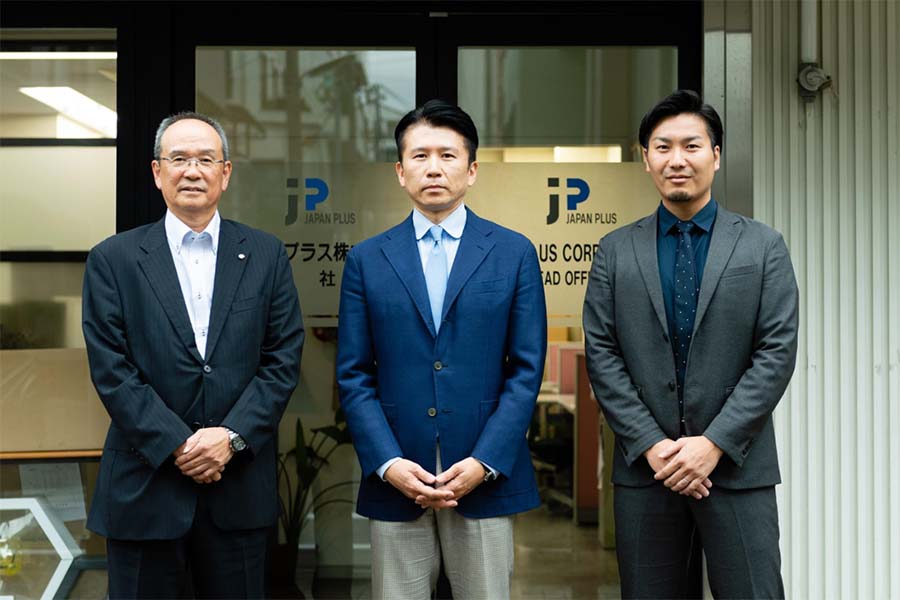
中央:ジャパン・プラス株式会社 笠倉大二郎専務取締役
右:サーキュレーション コンサルタント 土井啓義
製造工場の生産計画改善案件におけるまとめ
課題・概要
営業と製造現場の情報連携に課題を感じていたものの、正しいノウハウがなく、最適な改善方法がわからなかった。本質的な課題特定からプロ人材に依頼をしたいと決めて数社から紹介を受け、最終的に前向きな解決策を提案してくれた南波さんがアサインされた
支援内容
- ヒアリングを行なって工場の現状を把握。最適な生産計画が立てられていないことが課題として明確になった
- 数ヶ月かけて専務と現場リーダーに工場経営の考え方を伝授。原価管理の考え方や在庫がキャッシュフロー経営に与える影響について教育した
- 製造に関する部分は全て工場に責任を持たせるため、材料の調達、管理及び生産計画は工場で行うなど「会社のしくみ」にメスを入れた
- 現品管理を徹底し、日次/週次/月次で生産量、在庫をしっかり管理できるように「見える化」した
- 南波さんが現場を巻き込み、現場の納得度と理解度を上げ、生産計画を作成し必要な量を必要なタイミングで発注していく体制に変更
成果
- 月末の在庫が3割削減され、年間600万円近くのキャッシュフロー改善に貢献
- それまでは製造だけに没頭していた現場だったが、生産の「見える化」によって工程のルールが浸透。現品管理を徹底できるようになった
- 会社に工場経営のノウハウが蓄積し、現場で施策を考え専務がその監督を行う役割分担が可能になった
- 「見える化」の重要性を理解する工場文化を作り上げることができた
支援のポイント
- 原価管理の考え方など、自身の仕事が会社の数字に与える影響を理解できるようになるだけで現場の意識は大きく変わる
- 時代の変化により大量生産から受注生産にシフトしつつあるにも関わらず、旧態依然の生産を行っていた工場が、適正な利益を生み出す体制作りをスピーディーに実践するには、プロ人材に経験知見をインプットしてもらい実践でアウトプットしていく方法が有効
- 生産の「見える化」により生産性は大きく改善され、仕組みが上手く現場に浸透すれば自分たちで回していける。その際には経営陣、リーダー陣が主導していくことが大切
企画編集:新井みゆ
写真撮影:樋口隆宏(TOKYO TRAIN)
取材協力:ジャパン・プラス株式会社
※ 本記事はサーキュレーションのプロシェアリングサービスにおけるプロジェクト成功事例です。